AC Repair – How to Keep Your AC System Running Properly
A professional technician thoroughly inspects your air conditioner during a routine maintenance appointment. This thorough assessment helps them identify any potential issues or wear and tear that might cause a breakdown in the future.
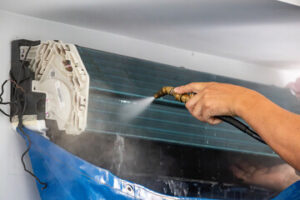
This preventative process helps you avoid expensive AC Repair Round Rock costs in the future. It also ensures your home is always comfortable for your family.
The condenser is one of the most critical components of an AC system. It takes the high-pressure refrigerant that comes in gaseous form from the compressor and transforms it into a liquid state so that it can transfer heat from your home to the air. It does this by passing the refrigerant through a series of coils that are arranged to maximize heat transfer efficiency.
If the airflow through the condenser is obstructed, your system will have a hard time cooling your home effectively. The best way to keep your condenser clean and in good working condition is to have your HVAC technician clear the area around it on a regular basis. This will help ensure that it is always working at maximum efficiency.
A faulty condenser unit can put a lot of strain on the rest of your system, leading to poor performance and possibly premature failure. This is why it is a good idea to get a high-quality condenser for your system if you are replacing it. It will work better with the air handler and will last longer, saving you money in the long run.
Among the most common AC repair issues is that the condenser coils are dirty. This can be caused by a variety of factors, including dirty air filters, clogged ducts, and low refrigerant levels. The good news is that cleaning a condenser coil is relatively easy for an experienced technician.
Another common problem is that the condenser fan is not working properly. This may be due to a blown capacitor, bent blades, or a dead motor. It is possible to replace the fan motor or blower assembly on an existing condenser, depending on the cause of the problem.
An increase in leaks from the condenser is also a sign of a faulty unit. This can lead to a loss of refrigerant, which is not good for your compressor or your system as a whole. A leaking condenser can also damage your home’s ductwork and lead to a reduction in indoor comfort.
Keeping your condenser clean and getting it repaired promptly by a professional AC repair company can help ensure that it stays in good working condition. Regular maintenance and inspections by an experienced technician will help reduce your system’s breakdown rates.
The Evaporator
Your AC evaporator coil is a crucial part of your system. Its absorption of heat from the air within your home is what starts the cooling process. Unfortunately, your evaporator coil can develop problems that affect the overall performance of your AC. The best way to keep your evaporator coil and the rest of your air conditioning working properly is to perform routine maintenance.
Located inside your air handler, the evaporator coil is made of metal and features U-shaped metallic tubes that easily absorb the warm air from your home. It also has metal “fins” that help the refrigerant circulate around the coil. This cools the refrigerant and turns it into a cold vapor that’s transferred to your condenser coil for further cooling.
A number of factors can cause your evaporator coil to develop a problem. One of the most common is a dirty air filter that can clog the coil. The clogged filter restricts airflow and causes the evaporator coil to work harder to cool your home. The evaporator coil can also be damaged by physical damage such as bent fins or electrical problems that result in short circuits.
Other issues that can negatively impact your evaporator coil include a faulty defrost cycle that prevents ice from forming on the coil, low levels of refrigerant fluid and corrosion of the metal coil. A frozen evaporator coil is often a sign that you need immediate AC repair.
The good news is that there are several things you can do to avoid problems with your evaporator coil, starting with regular maintenance. Changing the air filter two to three times per year will help reduce the amount of dirt that gets into the coil. You can also clean the outdoor unit of your AC and remove any vegetation or leaves that may be blocking its airflow.
However, repairing an air conditioner evaporator coil can require specialized tools not typically found in the average household toolkit. In addition, it’s important to work with a certified and trained professional who can perform the task quickly and efficiently.
The Compressor
The compressor is the heart of an AC system. It carries refrigerant from the condenser to the evaporator, which then cools the air in your home. The compressor is also responsible for absorbing heat from your home and transporting it to the condenser. Without a properly functioning compressor, your system cannot cool. A variety of issues can interfere with the operation of your air conditioning system’s compressor. These include:
A failing fan inhibits heat transfer and can cause your AC to shut off. This means that a repair or replacement fan is needed to keep your air conditioner running.
Blocked suction lines can also prevent your compressor from cooling properly. When these lines are too small, they restrict the flow of refrigerant into your compressor. This can overwork the unit, causing damage and resulting in a higher than normal energy bill.
Low refrigerant levels are another common AC problem. These are often the result of a leaky compressor. Fortunately, this can often be repaired by an experienced technician.
Strange odors can mean a problem with your compressor or ductwork. The odor may be caused by a clogged filter or dirty coils. It could also be the result of a problem with your thermostat. Regardless of the source, a professional inspection should be performed to ensure that your ducts are properly sealed.
Your AC technician will inspect the compressor for signs of a mechanical problem and replace any components that need it. This is why it’s important to schedule regular maintenance visits with a trusted HVAC company.
When you’re evaluating an AC repair company, look for one that is accredited by professional associations. This will offer proof that the technician is qualified to perform the work. Additionally, look for technicians who provide an in-person assessment of your system and propose solutions before giving you a quote. This way, you’ll be sure that the technician isn’t simply trying to sell you a new AC system. The assessment will also reveal other potential problems that you can have fixed before they become bigger ones. This can save you a lot of time, money and headaches down the road.
The Thermostat
The thermostat is the brains of your entire HVAC system. It keeps track of the current air temperature in your home and then tells heating and cooling equipment to turn on and off as needed. It’s also responsible for keeping track of the desired temperature settings, which can vary from room to room. Because of its critical role, it’s important to know when something might be wrong with your thermostat.
Thermostat Display is Dim or Blank
If your thermostat display screen goes dark, it could be a sign that the unit isn’t getting power. Check the batteries and the breaker in your home’s electrical panel to ensure that neither has been blown or tripped. If the problem persists, remove the thermostat cover and inspect for a dirty display screen, faulty wiring or loose screws.
Temperature Is Not Reaching Setpoint
If you’re still having trouble with your thermostat, it’s time to call for an AC repair technician. If your programmable thermostat isn’t following your pre-set temperatures, it may need to be replaced. An experienced technician will be able to find the right solution and replace it for you.
Alternatively, you might need to clean the unit itself or make sure that the vents aren’t blocked by furniture or other objects. A clogged or dirty filter can also restrict airflow and cause your cooling unit to overwork, which could lead to premature wear and tear.
Cooling Unevenly
If some rooms in your house feel cooler or warmer than others, it may be a sign that the ductwork needs to be cleaned, or the thermostat isn’t functioning properly. Thermostats often have error messages on their screens that name the problem, but older ones can also experience problems due to faulty wiring or old age.
You should never attempt DIY thermostat repairs. This is a task best left to an expert, since the device contains electrical connections that can cause bodily harm if you get it wrong. The good news is that our professional technicians can diagnose and fix any issues with your thermostat quickly and safely, so you don’t have to deal with the discomfort of an AC unit that doesn’t work as it should.
Window Installation Basics
Window Installation In Austin is a fairly simple project for many contractors. However, every brand of window has different instructions that must be followed.
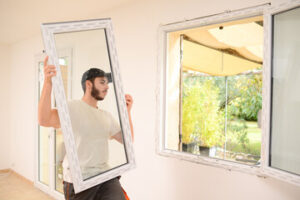
The first step is to roll house wrap over the window opening. This prevents water and cold air from entering the home. A backer rod is installed next. This eliminates thermal bridging and seals the nailing flange.
Measurements will be needed to determine the size of your replacement window. While it is possible to do the measurements yourself, a professional will be able to take into account your unique home structure and potential frame adjustments.
Before starting any measurements, ensure that the old window is closed and that any screws holding the sash in place are removed. This will prevent any errors caused by uneven or inaccurate measurements. Additionally, make sure to clean the area around the window frame and sash to remove any debris or old putty that could interfere with the measurements.
Begin by measuring the width of your existing window opening. Position your tape measure horizontally between the left and right jambs at the top of the window, then move down to the middle of the window and finally, to the bottom. Record the measurements and highlight the smallest one, as this will be used to determine the width of your new window.
Next, you will need to measure the height of your existing window opening. Start by positioning your tape measure against the head jamb (the top horizontal board that sits above the window) and extend it to the bottom window sill. Do not confuse the window sill with the window stool, which is the bottom trim section that extends into the room. Repeat this process on the left, middle and right side of the window. Once again, highlight the shortest measurement, as this will be used to determine the height of your new window.
Lastly, you will need to measure the depth of your existing window opening. This will be determined by the distance between the inside window trim and the outside window stop strip. It is important to ignore any parting beads or trip strips in the window opening when taking these measurements.
Once you have recorded the above measurements, you will be able to order your replacement windows. Remember, to keep in mind that the height and width of your new window should be slightly smaller than the measurements taken for the existing frame to allow for shimming and insulation.
Removing the Old Windows
If you’re having new windows installed, the old ones must first come out. Depending on the type of window, it may need to be removed from the inside or outside. Canvas runners and tarps will be set up throughout your house to protect the floor from debris. This is an extra step we take to ensure your home remains clean and safe for the crew while they work.
The crew will start by cleaning the previous sealant areas that kept the old windows in place. They will also remove any molding that is on the outside of the frame or sill and the sash. They will then cut away any shims that were used to keep the window in place, as well as the jamb liners and parting beads on older wooden windows. If the new window is a full-frame replacement, they will also remove the trim around the window opening to ensure it fits correctly.
Insert replacements, on the other hand, use an existing frame and simply add a new sash to replace the old one. This is a less invasive installation method, which minimizes any disruptions to the wall and trim. This type of replacement is a good choice for historic homes or for homeowners who don’t want to address the exterior of their home.
Once the old windows are out, they’ll be removed section by section or room by room. This helps the crew stay on schedule and prevents having an entire room open while they wait for another part of the house to be completed. It’s also a great way to make sure the crew is not working on any windows that don’t need replacing. A tape note will be placed on the windows that are not being replaced so there’s no misunderstandings between crew members.
The next step is to prepare the opening for the new window by applying beads of caulk along the bottom of the frame and on the top of the sill. This will ensure the new window has a water-resistant barrier that keeps moisture and rain from seeping through the interior of the house. Shims are also sometimes used to ensure the window is plumb and level. Lastly, the crew will apply any necessary insulation, as well as a weather stripping around the edge of the new window to help reduce energy loss.
Installation
You’ve done the hard work of researching window options, choosing a contractor, and making detailed decisions about your new windows. Now, installation day is fast approaching. Before the crew arrives, you should take the time to clear away items that could be moved and to cover any surfaces you’d like protected during the construction process. It’s also helpful to let the team know if you have pets on the property so they can use extra care when moving furniture or cleaning around them.
Your contractor will carefully remove the old sash from the opening, taking care not to break or damage the glass or the surrounding trim. Then, they’ll clean and prepare the opening for installation of the new window frame. They’ll remove any caulking or sealant that’s holding the old frame in place. They’ll also clean off the sheathing, brick, sheetrock, and any other materials that are surrounding the window opening to make sure it is smooth, free of debris, and ready for the installation.
During window installation, the installers will measure and cut the frame to fit the size of the opening. Then, they’ll install the window in the opening and secure it with long screws through the main vertical sides of the frame known as jambs. After the window is set, the installers will caulk and seal the interior and exterior to promote energy efficiency, protect the windows from water, and ensure there are no gaps or leaks that could compromise the performance of the windows.
The final step in the window installation process is a walkthrough with your crew leader to make sure everything fits perfectly and functions properly. They’ll explain how to operate your new windows, show you how to clean them, and answer any questions you may have. They’ll then haul away and dispose of your old windows and any other leftover debris from the work area. They’ll also thoroughly clean up all areas where they’ve worked so it looks as if they never even came inside your home. This is a mark of a high-quality contractor.
Clean-Up
Whether you’re replacing one window or upgrading your entire home, renovation projects are messy. But it’s important to focus on clean-up afterward so that your home looks as beautiful and functional as possible. Especially when it comes to your windows, dirt can build up over time, causing unsightly stains and hindering the function of Low-E glass. Cleaning your windows regularly is essential, and this is where a professional can help.
Before the installation begins, the contractor will make sure that the opening is free of debris and caulking. They may use a utility knife to cut through any sealant that’s holding the old window in place, but they’ll be careful not to damage the surrounding frame or wall. They’ll also clear away any sash or frames that aren’t part of the new window, and they’ll recycle and dispose of the old materials.
Once the removal process is complete, the contractor will sweep and mop the area around each window to clean up any dust or dirt that’s accumulated. They’ll also take steps to protect surfaces in your home, such as floors and furniture, from construction debris by using drop cloths and plastic sheets. They’ll also create paths throughout your house so they can work more easily and minimize the amount of debris that’s spread around the home.
To keep your windows clean, you’ll want to mix together a simple solution of vinegar and water. This should be enough to remove most dirt and stains from the glass, but it’s always a good idea to add a little rubbing alcohol to your cleaner for stubborn spots. Adding a few drops of dish soap to your mixture can also help disperse grime and leave your windows looking sparkling clean.
While it’s not necessary to wipe down your window panes after every washing, you should definitely do so once a week or more. The more you use your windows, the more they’ll need to be cleaned, and a yearly deep clean is a good investment for keeping your windows as beautiful as possible. And don’t forget about your outdoor windows, either—they can be just as dirty as indoor ones.
Boat And RV Storage Is A Profitable Addition To Your Self Storage Business
Boat And RV Storage Owasso is a profitable addition to your self-storage business. This type of storage provides unique amenities, such as dump stations and power outlets in individual spaces, that make it appealing to customers.
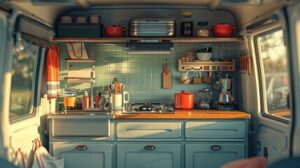
Customers looking for boat/RV storage are willing to travel further than a traditional self-storage customer, so site design and marketing are different.
Boat and RV storage is a growing business. The demand for such facilities is likely to increase as more people purchase recreational vehicles. These vehicles require special accommodations, such as higher clearances and a larger parking lot size. These amenities are often expensive to build and maintain. They also affect the price of storage space. However, if you know the market, and understand how to manage these facilities, they can be profitable for your company.
When it comes to building a Boat and RV storage facility, the most expensive aspect is the land price. This is particularly true for facilities located in urban areas. You will have to spend a large amount of money on acquiring the necessary land, and you may also need to pay for grading and utility expenses. You should also consider other costs, such as construction management and landscaping.
The cost of building a Boat and RV storage facility varies depending on the type of construction you choose. You can build a boat and RV storage facility with internally demised spaces, open warehouse space, or multiple-story climate-controlled space. According to Self-Storage Ninjas, the average cost per square foot for an internally demised Boat and RV storage space is $55 to $65.
These facilities are often located near ocean harbors, lakes, rivers, or river ports. They can be designed for ocean-going vessels that do not come with a trailer, or they can be built to accommodate boats that are extracted from (and returned directly into) the water using large slings. These facilities can offer a wide variety of pre- and post-departure services, including shrink wrapping, washing and detailing, detailing the interior, shampooing the carpets, turning on the refrigerator 24 hours before departure, and more. These services are typically included in the rental fee, while others are offered on an a la carte basis.
Boat and RV storage can be a lucrative business, but it requires planning and a large piece of land. You should also determine your target market and whether you want to sell space to luxury markets, RV owners, or casual boat and RV owners. In addition, you should be aware of the complexities and risks associated with this business.
Security
A reputable boat and RV storage facility will take security measures seriously. They will offer secure facilities with gated access and onsite management to ensure the safety of your vehicle. They may also provide indoor or outdoor storage options, depending on your preferences. They may also offer climate control and other amenities to make your storage experience as enjoyable as possible.
With the increased popularity of recreational boating and RV travel, the need for specialty storage facilities has grown. These facilities serve as a valuable service for these expensive vehicles by providing a safe place to store them between uses. However, they are often targets for theft and other forms of crime. As a result, many specialty storage operations are investing in enhanced door security and other advanced security features to meet the needs of their premium tenants.
To meet the demands of their customers, boat and RV storage operators must balance exceptional security with tenant convenience. This is particularly true for operations that offer RV and boat storage in conjunction with traditional self-storage units. Tenants expect seamless site and unit access, and they will become frustrated if they have to repeatedly enter and exit large trailers or other vehicles. The key is to identify opportunities to bolster security while streamlining common specialty storage activities, starting with seamless entry and exit at authorized access points.
Adding an alarm system is another effective way to improve the security of a storage facility for boats and RVs. These systems can be used to notify staff or the police if they detect unusual activity in the facility. Additionally, they can help deter criminal activity by alerting potential perpetrators that their actions are being monitored.
The right alarm system will also include a remote monitoring feature. This allows the operator to view camera footage from anywhere, even when they are off-site. This can be a powerful deterrent for burglars and other criminals, as it will give them a greater chance of being caught on camera. In addition, these systems often come with a web interface that can be accessed by owners and managers from different locations.
Amenities
When it comes to offering boat and RV storage, there are many amenities that can help differentiate your business. For instance, you can provide a wide variety of services, such as detailing, cleaning, and even repairing. This can help to boost your revenue and attract more customers. You can also offer temperature and climate control units to keep your customers’ vehicles safe in harsh conditions. Another important factor to consider is location. This is especially important if your facility is located near popular recreational areas such as national parks or lakes. You can use this advantage to your advantage and promote your storage units as a convenient place to store boats and RVs.
In contrast to traditional self storage, boat/RV storage is a niche that requires unique marketing strategies. This is because these types of items are usually much more expensive and are often used for longer periods of time. Additionally, they are less likely to be discarded when the owner no longer needs them. This is why it is important to research the potential demand for boat and RV storage in your area before investing in this type of property.
Unlike self-storage, boat/RV storage is typically located farther from residential homes than traditional facilities. This is because homeowners associations frequently forbid these vehicles from being stored in driveways or on the street. As a result, customers tend to look farther out of town for a storage location.
It is important to consider the location of your boat/RV storage facility, as well as its accessibility and security features. You should also consider the cost of running the facility, as well as the amount of income you can expect to generate. Additionally, you should look at any local regulations regarding boat and RV storage.
Many people find that boat/RV storage is a better option than storing their vehicle at home because it provides them with more privacy and security. Moreover, these facilities offer a variety of amenities such as electric hookups for boats and RVs, dump stations, wash stations, and dog parks. These amenities can make it easier to maintain your vehicle and make it more fun to drive. In addition, they can help you save on fuel costs.
Location
RV and boat storage are a unique and growing market opportunity that can be either stand-alone or successfully tied to traditional self storage. However, this product type requires a different set of customer requirements and should be considered as a separate niche in your market strategy. A successful site will require the right mix of amenities and a strong marketing program. In addition, rezoning to permit this use may be necessary. Careful planning and engagement with local officials can help guide the zoning process.
Unlike traditional storage customers, who look for locations within a few miles of their homes or workplaces, RV and boat storage customers are willing to travel farther distances to find a suitable storage facility. This can be an advantage if the location is near a campground, lake or other recreational destination. It is also possible to build a profitable RV and boat storage business on a less expensive piece of land than a typical self-storage property because the facility doesn’t need to have a lot of parking spaces per acre.
With communities cracking down on boats and RVs parked in driveways and yards, and with the popularity of jet skis, it’s important to offer these customers an alternative. Many people will store their boat or RV in a storage facility to keep it out of the elements and ready for the next time they hit the water. To serve this need, you should consider offering outdoor and covered storage options for these vehicles.
In addition to choosing the right size and type of RV and boat storage stalls, you must also plan the layout of your property. This includes determining prevailing traffic directions, daily traffic counts and exposure to adjacent thoroughfares and commercial centers. If the rezoning process is required, careful coordination with local planning officials and engagement with community stakeholders can help mitigate concerns and avoid delays.
Once upon a time, most RV and boat storage was little more than dirt fields roped off by padlocked chain-link fences. Today, this niche is a significant part of the self-storage industry, with operators integrating self storage disciplines and adding modern amenities to attract tenants and maximize profits.
All About Recycling Demolition Waste
Construction and demolition wastes can be recycled into useful products and materials. This can save money, promote sustainability, and preserve natural resources.
In an ideal scenario, C&D debris could be reused or salvaged on the same project site. Although the hierarchy of waste minimization lists reducing and reusing as higher priorities, recycling is an important way to conserve resources.
Reuse
Using construction and demolition materials that are no longer needed reduces the amount of new resources that need to be mined, cut down, and transported. This helps to cut down on pollution, resource depletion, and climate change. It also helps to save money for building projects. This type of waste management can be done in a variety of ways including reuse, recycling, or salvaging.
Construction and demolition debris, or C&D waste, is the material generated by undertakings ranging from the construction of residential homes to the deconstruction of international airports. This material makes up a large percentage of the trash that is sent to landfills. Fortunately, most of this material can be reused or recycled. This extends the life of natural resources such as lumber, drywall, metals, and concrete, and it also reduces disposal costs.
Most of the materials can be reused directly on the site, but some may need to be sorted before they can be used again. This can happen either on the site as a form of deconstruction, or it can take place off-site at a sorting location, or at a C&D recycling center. The process of separating these materials into their respective categories also allows for the identification and removal of any hazardous materials. This can help to prevent toxic substances like lead from poisoning water supplies or plasterboard from releasing hydrogen sulfide in landfills.
The best way to reuse C&D waste is to reduce it at its source, through the use of practices like waste minimization, source reduction, and reuse. This is achieved through deconstruction and by implementing other measures such as design for disassembly on building sites, or designing products with a longer lifespan. This will also enable the recycling of these materials once they have reached the end of their usefulness.
Some governments have put into place incentives that promote this kind of waste management. For example, in San Jose, California, developers of new buildings need to pay a fee proportional to their project size, and this can only be refunded if they divert a certain percentage of the debris.
Recycle
Construction and demolition wastes contain multiple economically valuable materials that could be recycled instead of using new, raw materials. These include reusable aggregates, bitumen, concrete, wood and metals. They can be recycled into a wide range of products, from construction materials to energy production. This is especially important in a time where our global supply of natural resources is rapidly declining and becoming scarce.
However, many C&D materials are not easily recycled due to traditional demolition practices and the way in which these materials are typically handled on a project site. These types of projects frequently generate a blend of mixed rubble that makes it difficult to extract and sort reusable materials. This makes it difficult to meet recycling goals later in the process and can lead to the need for additional costs.
Fortunately, the majority of C&D materials are actually recyclable. Steel is a prime example of this, with about 98 percent of steel structural framing material avoiding landfills through recycling. Other common recycled materials in construction and demolition debris include drywall, carpet, paper and cardboard, wood, and various metals. This means that if we are able to properly sort and store C&D materials on-site, we can achieve a high level of recycling.
In order to recycle C&D materials, they must be separated into distinct categories on-site or at the recycling plant. Having separate boxes for each type of debris is the best method for achieving recycling goals, as it provides instant feedback to employees on-site about their efforts and is the easiest way to monitor diversion rates.
On-site separation also allows for better control over the recycling operation and can reduce the amount of materials that must be transported off-site, reducing transportation and logistics costs. In addition, separating materials on-site can help to foster a positive work culture in which everyone is responsible for the environment and is working to minimize waste.
It is also crucial that contractors follow proper construction procedures when handling C&D materials. This includes ensuring that all workers are wearing the required safety equipment, as well as conducting regular inspections of waste management and disposal practices. This will not only improve a contractor’s environmental image but can also help to reduce their liability risks.
Salvage
Over 600 million tons of construction and demolition (C&D) waste was generated in the United States in 2018. This figure represents about double that of generated municipal solid waste. While the majority of C&D debris is destined for landfills, many materials can be salvaged and used for other purposes. For example, wood and other lumber products can be repurposed as landscape mulch, shredded and turned into boiler fuel, or chipped into road base for new pavement. Metals, gypsum wallboard and flooring can also be recycled into new products.
Recycling and reuse of building materials not only reduces our reliance on natural resources but also saves money in the form of reduced disposal costs. In addition, repurposed building materials can have a unique look and feel that adds character to a space or project. In fact, using repurposed building materials can be even cheaper than purchasing new materials for the same project.
Repurposing building materials is one of the most effective ways to cut down on demolition waste. A successful repurposed building project requires thorough planning and the help of a knowledgeable team. For instance, a developer can prioritize waste reduction by implementing pre-demo cleanouts and soft stripping of existing structures to identify usable materials. This enables the demolition team to plan accordingly and reduce the volume of material that will need to be hauled away for disposal.
Other effective practices to minimize building-related waste include implementing a source separation strategy on jobsite, utilizing a sortline or pick line to rapidly separate waste and recyclable materials, and incorporating deconstruction into demolition projects to preserve usable components for reuse. Additionally, a company can take advantage of the growing demand for construction and demolition materials by selling their scrap or salvage rights to local recyclers.
To make the most of your demolition project’s potential, consult a waste management expert to learn more about sustainable and innovative practices. You can find experts in the industry through recycling organizations, government agencies and private companies. A good place to start is WM’s LampTracker program, which makes it easy for businesses to recycle bulbs, batteries, electronics, medical waste and mercury-containing items.
Donate
When materials are donated to reuse outlets, they may be eligible for a tax deduction. This can help keep demolition waste out of landfills and support the local economy. It’s important to consider this option when planning a project. Some projects are better suited for this approach than others, such as projects with large quantities of gypsum wallboard or ceiling tiles. In these cases, it may be helpful to have a specialized truck dedicated to collecting reusable materials and sitting it at the job site until they can be removed for donation. Identify potential reuse outlets in advance by reaching out to reuse stores.
Hello world!
Welcome to WordPress. This is your first post. Edit or delete it, then start writing!